I first met Mike Taylor six years in the past, and since then I’ve adopted the expansion of Taylor Toolworks, the corporate he cofounded together with his brother Dan. Over time, it has turn into a go-to vacation spot for woodworkers in search of distinctive instruments for shaping, measuring, and crafting. Along with a various catalog, the corporate has ventured into importing hand planes from India. Simply earlier than the vacations, Mike despatched me two fashions from Taylor’s newest line: Bedrock-style bench planes made with a mix of ductile forged iron, brass, mahogany, and metal.
This submit gives you a way of those new instruments and their potential, in addition to some minor drawbacks. It additionally presents steering for readers who buy these planes on easy methods to fine-tune them into formidable shaving instruments.

The Bedrock Aircraft Type
To understand the importance of the Bedrock-style aircraft, it’s price understanding what units it aside. Stanley Bedrock planes are famend for his or her distinctive design and performance, setting a benchmark in woodworking instruments. In contrast to conventional Bailey-style planes, the Bedrock’s modern construction permits customers to regulate the throat opening effortlessly with out disassembling the blade and cap iron—a comfort that saves time and preserves changes. The meticulous casting and precision milling of those planes creates a seamless iron-to-body connection, successfully minimizing chatter and delivering smoother, extra dependable efficiency. These qualities have solidified the Bedrock as a cornerstone of superior aircraft design, revered by woodworkers for over a century.
Stanley manufactured the primary Bedrock planes in america and saved producing them for a couple of many years, however then the corporate scrapped their manufacturing. Within the final decade of the twentieth century, Lie-Nielsen Toolworks determined to resurrect the Bedrock design and open a line of aircraft manufacturing in Maine that produced the perfect Bedrock planes ever made. Following Lie-Nielsen, Clifton in England initiated its personal type of Bedrock planes. Then within the mid-2000s, Woodcraft launched its personal Chinese language-made line of Bedrock branded as WoodRiver. Till now, this unique group of producers—one in america, one in Britain, and one in China—managed the pristine and costly Bedrock market. However with India’s emergence as a big industrialist nation, an Indian instrument producer has determined the time is true to enter this top-tier woodworking hand-tool market.
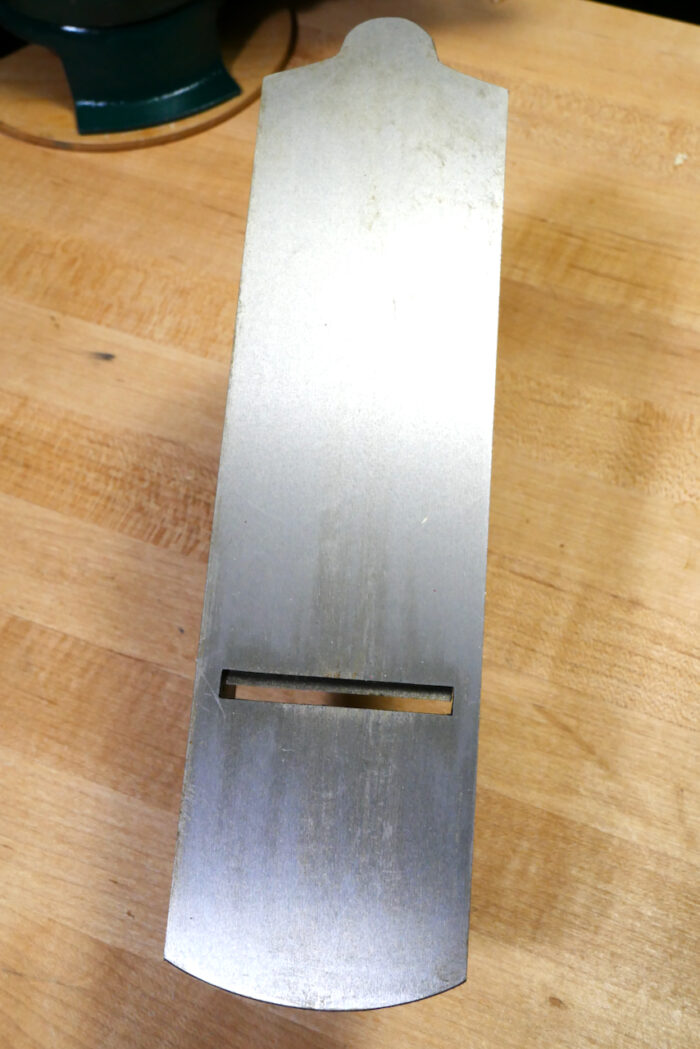
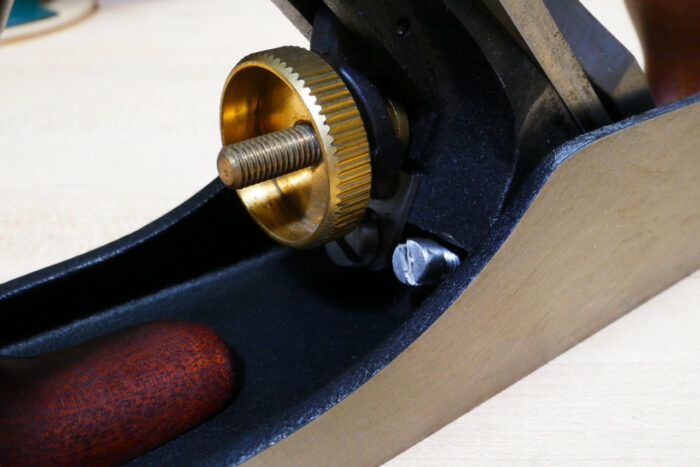
The Taytools Planes
Mike Taylor despatched me two fashions: a #4 smoother and a #5 jack aircraft. Each planes’ our bodies are fabricated from ductile forged iron, with the frog and cap iron constructed from the identical materials. The frog’s clamp-down studs, locking screws, center adjuster screws, and yoke are metal, whereas the central cap-iron screw, adjuster nut, and picket deal with nuts are brass. After cleansing, oiling, sharpening the blade, and testing the planes, I can confidently say these newcomers are exceptionally properly made and, given their value, supply a compelling quality-to-price ratio. Beneath, I define the steps I took to fine-tune these planes for optimum efficiency earlier than first use.
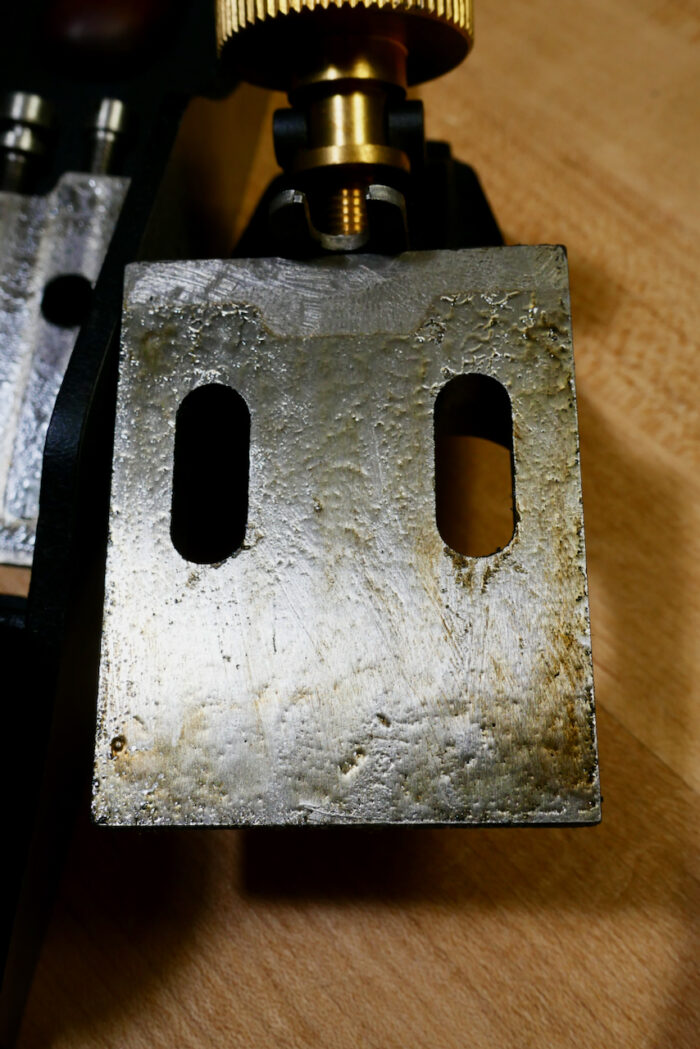
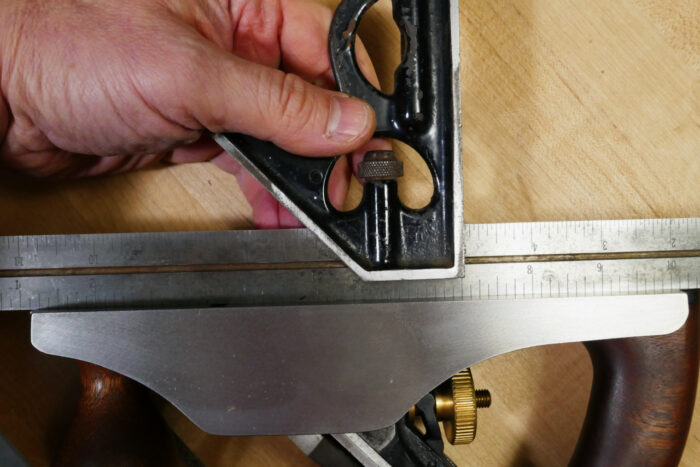
Flatness
The aircraft’s sole is completely flat. I checked it with a straightedge and was impressed with its trueness alongside the size and throughout the only. The frog’s ramp can be completely straight; actually, that floor was lapped and appears pristine.
![]() |
![]() |
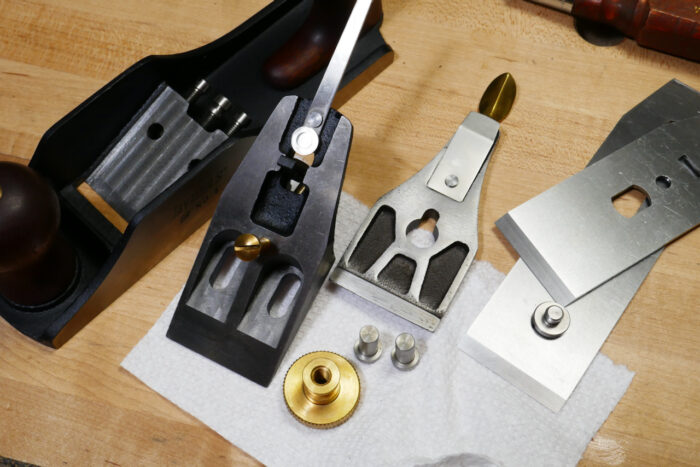
{Hardware} and Lubrication
Whereas the machining is spectacular, post-milling cleansing and lubrication left room for enchancment. Thick lubricant lined all lapped surfaces and wanted cleansing with mineral spirits. Nooks and crannies have been crammed with black residue from the milling course of, which I eliminated utilizing brushes, Q-tips, and rags.
Particular consideration was wanted for the holes by which the frog’s clamp-down studs nest. These studs, important in all Bedrock planes, cross by way of the aircraft physique and safe the frog by way of locking screws. After cleansing the holes, I utilized oil to the studs’ shafts and heads and added grease contained in the conical holes. This grease improves the motion of the locking screws, which push into these conical recesses to maneuver the studs downward and maintain the frog firmly in place. I additionally spent a couple of minutes deburring and chamfering sharp corners on the frog’s oval studs’ slots. Lubricating all different transferring elements ensured clean operation throughout use.
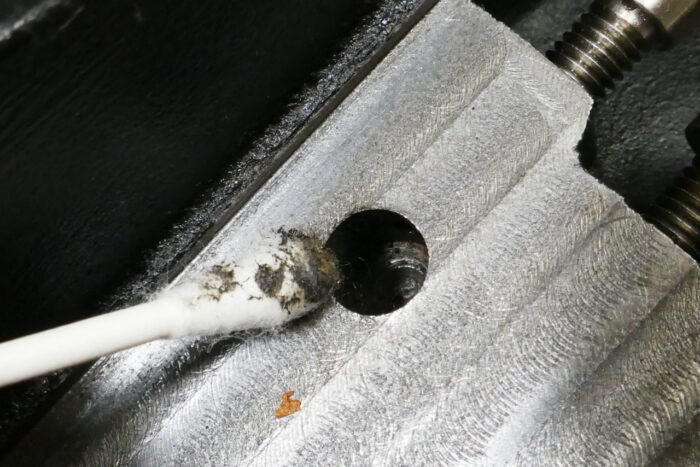
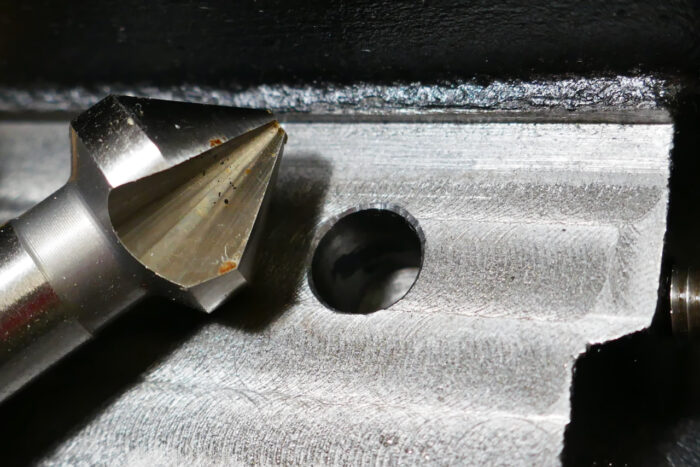
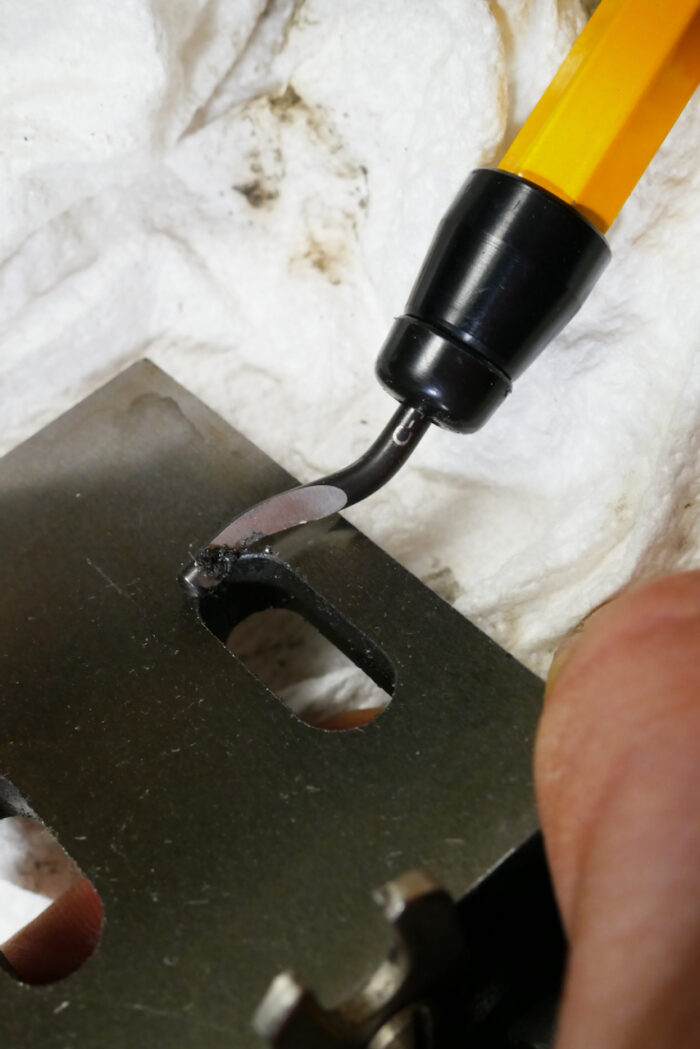
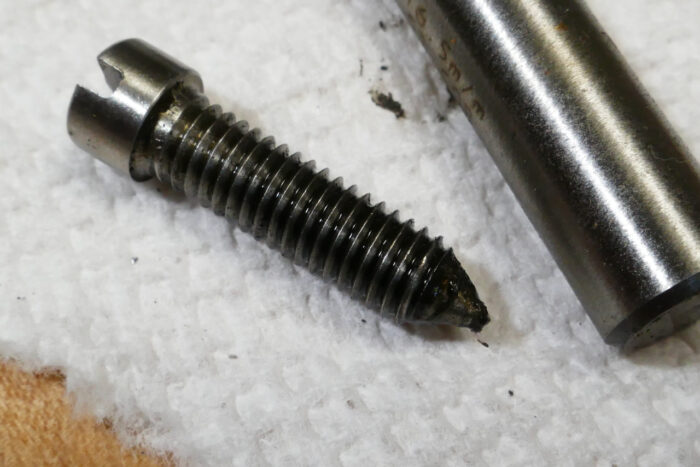
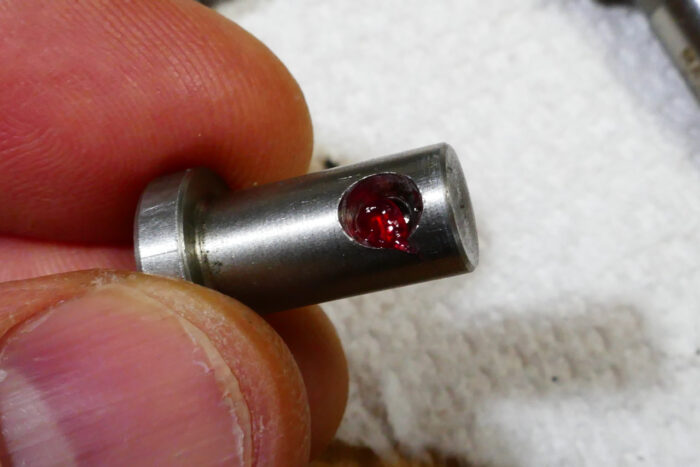
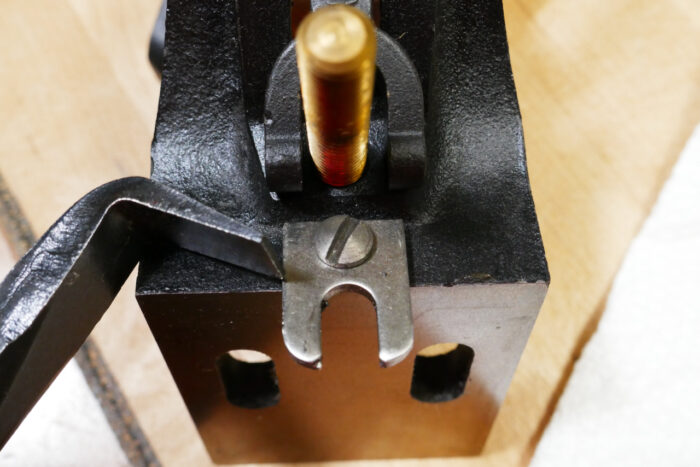
Blade Meeting
The again of the high-carbon blade wanted minimal lapping earlier than sharpening, and the thick and precisely milled chip breaker didn’t require any work.
Cap Iron
Whereas the #4 aircraft’s cap iron offered sufficient downforce with the pivoting of the cam lever over the manufacturing facility blade, after I changed the thicker blade with a thinner Hock blade, I wanted to regulate the central cap-iron screw twice. Like many hand aircraft customers, my go-to setup is to permit the cap iron to slip out and in from beneath the screw head and solely interact the cam lever to tighten the cap iron. Adjusting the screw to compensate for the completely different blade thicknesses is regular, however I had to do that twice. After connecting a Hock blade to the chip breaker, I positioned the blade over the frog and slid the cap iron underneath the screw head. Then I turned the screw to the purpose the place it nearly touched the chip breaker. After I pivoted the cam lever and anticipated it to offer good downward stress, I seen that it didn’t create ample pressure, so I needed to launch the stress and tighten the central cap-iron screw an extra flip, then pivot the cam lever—this time, creating sufficient downward stress.
|
|
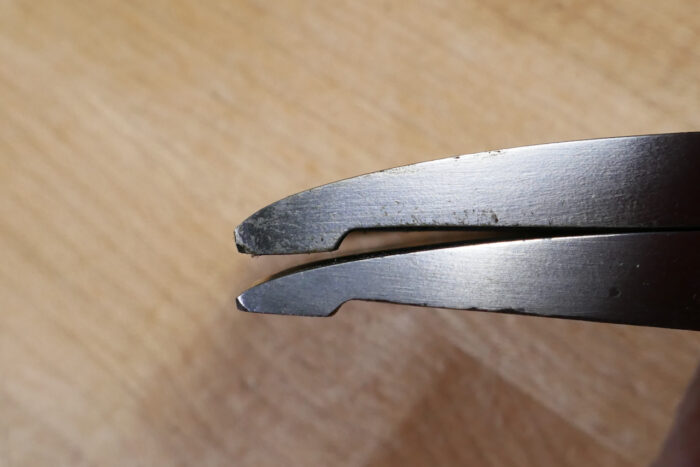
In distinction, the cam lever of the #5 aircraft had a bigger radius, which labored completely on the thinner blade and required only one screw setup.
The underside line is that you simply may must futz round with the cap iron’s central screw when you resolve to interchange the thick manufacturing facility blade with a thinner one. Nevertheless, when you follow the manufacturing facility blade, you’ll be positive. That stated, in order for you a heftier blade, more durable than the one offered, Taylor Toolworks sells premium blades similar in thickness. These aftermarket blades are rated Rockwell’s 60-62.
|
|
Yoke Backlash
The yoke design is sweet, with a pommel-like enlargement on the prime to clean the contact with the chip breaker’s slot. The blade’s advancing and retracting have a slight backlash slack, greater than I skilled with my Lie-Nielsen aircraft.
Submit-Buy Modifications You Can Do Your self
The frog retention studs/pins in my Lie-Nielsen aircraft have an indent to indicate the situation of the conic gap. In the event you take away the studs or they fall out throughout a deep cleanout, these indentations will assist orient them again into their holes. It’s a minor factor, however it’s useful. For the reason that Taytools aircraft didn’t have markings, I created them utilizing a middle punch.
Testing the Aircraft
After cleansing and adjusting the aircraft, in addition to sharpening its blade, I examined it on laborious, smooth, and figured wooden. The Bedrock options proved to be very useful, particularly with figured wooden, as they allowed me to reduce the mouth (or throat) to beat difficult grain and stop tearout. I appreciated having the ability to alter the frog’s positioning with out lifting the cap iron and blade meeting, which made the method extraordinarily productive. I used to be additionally happy to be taught that the Taytools frog glides easily on its ramp with none noticeable lateral slack. Which means after repositioning it, you received’t want to have interaction the aircraft’s lateral adjustment to convey the blade again parallel with the only.
|
|
|
|
|
|
Ultimate Ideas
The brand new Taylor Toolworks planes are spectacular, efficient, and reliable. After cleansing, deburring, and lubricating, they carry out nearly in addition to these from established manufacturers like Lie-Nielsen and WoodRiver. At $120 for the #4 and $140 for the #5, they’re a discount. In the event you don’t thoughts getting your fingers soiled and greasy for half-hour of prep work, this new line of planes must be in your radar.
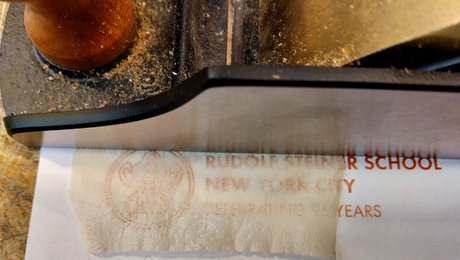
High quality instruments encourage excellence

Handplane Fundamentals: Sharpening

Restoring Handplanes: Sharpening and Setup
Wonderful Woodworking Really useful Merchandise
Veritas Precision Sq.
This precision sq. is extremely versatile, from checking squareness to dialing in machine setups.
Marking knife: Hock Double-Bevel Violin Knife, 3/4 in.
This heavy, double-beveled knife stays on monitor in all instructions, and works simply positive with out including a deal with.
Starrett 4″ Double Sq.
Head is straightforward to take away, exchange, and lock down; narrowest blade, at 5⁄8 in., made it simpler to suit into tight locations; laborious to learn underneath vibrant lights.
Join eletters at present and get the newest methods and how-to from Wonderful Woodworking, plus particular presents.